1Select Scanner
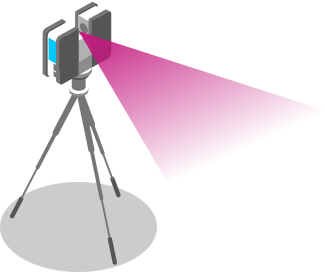
WELCOME TO OUR VIRTUAL WORLD
3D Laser scanning also know as HDS Surveying (High Definition Surveying) or LiDAR is a technology that uses lasers to measure and capture environments in 3D. Currently there are many different types of scanners each with varying speeds, accuracies, ranges, durability and general uses. At Digital we operate a fleet of equipment ensuing the best tool is used for the job in hand as no one scanner does everything.
No matter which scanner is used the basic principle is the same. A laser is fired out and for every surface that the laser hits a point in space is recorded (xyz). At the same time the scanner will record the reflectivity of the surface giving an intensity value, and nowadays most scanners also have in built cameras which provide colour and an rgb value to each point.
These points are captured at speeds of up to 1 million points of data per second creating a very dense point cloud of data.